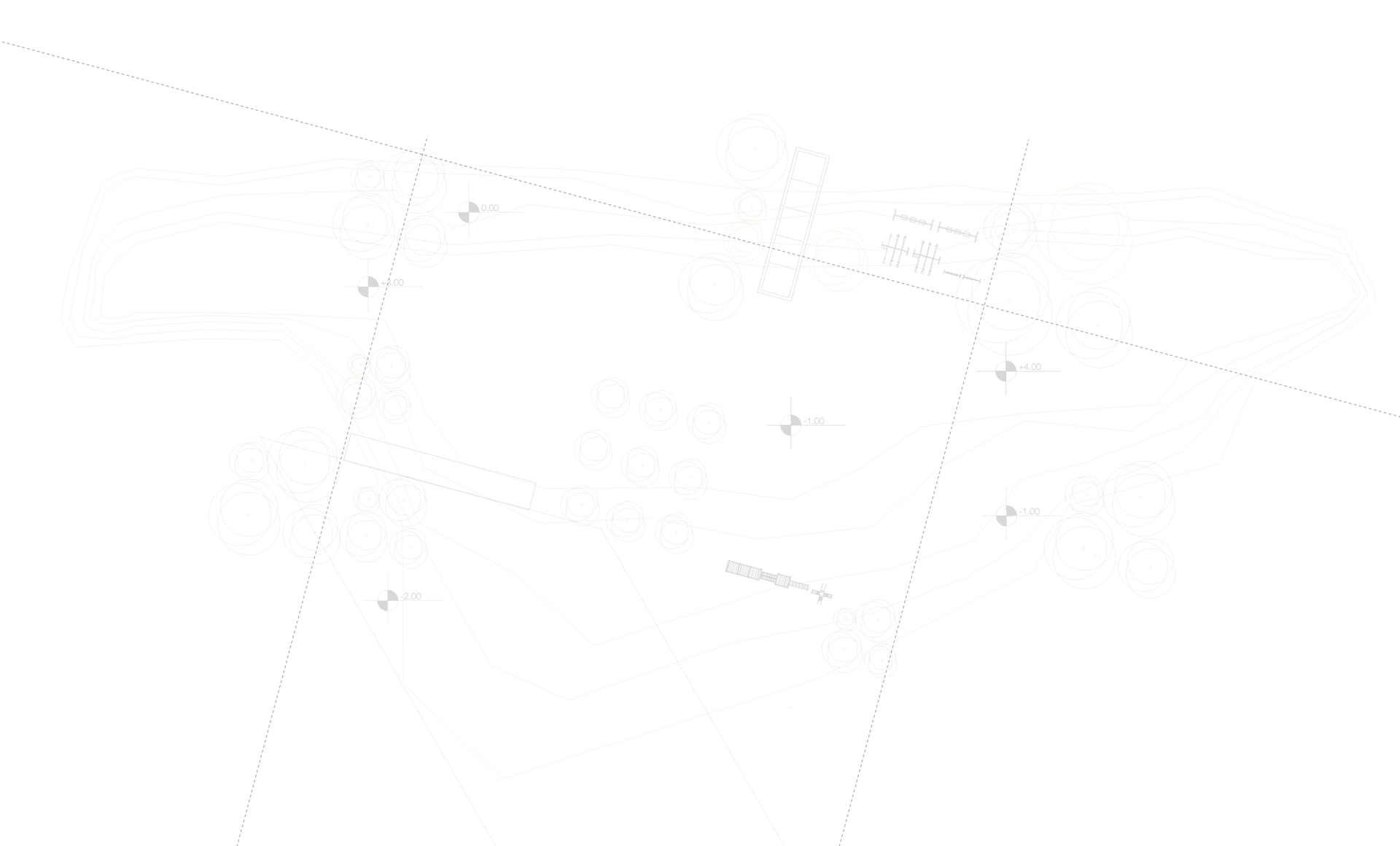
Results & Summary
As previously stated, our design is inpired by the Jellyfish motion. A common jellyfish such as the Aurelia Aurita ( "moon jellyfish") swims by jet propulsion. During the power stroke the muscular bell cavity contracts, ejects the water, and relaxes during the recovery stroke allowing the water to fill in the cavity for the next cycle. Because the strokes happen at different rates it allows an overrall displacement per cycle that enables it to travel.
The goal of this project is to build a jellyfish-like prototype using the popupCAD software and laminate manufacturing techniques. Our checkpoints show the development of our concept and some of the challenges considered through out the design process. The biggest challenge and catalytic factor in our design is to manufacture and actuate a laminate prototype that is waterproof. In order to accomplish this, we selected a Sarrus linkage as our mechanism since it can easily be actuated using a PAM (Pneumatic Artificial Muscle) (See Figure 4&5).
Our latest prototype is a (2x) smaller version of prototype 3 (see checkpoint 3). The prototype layers were planned using popupCAD software and were made of layers of polypropylene, polyethylene and double sided adhesive. The top and bottom layers are made of polypropylene which are the rigid layers. The middle, polyethlene layer is the flexible layer that acts as a hinge between the rigid linkages. The polypropylene and polyethylene were selected because they are waterproof and light-weight. A challenge we faced in the manufacturing process was to create a strong hinge connection between the linkages. Our original idea was to create hinges by stacking two sheets of PET bonded by adhesive but this would easily delaminate especially when placed in water. So we had to modify our manufacturing process to make the hinge a continuous layer of PET in order to create stronger hinges. (See Figure 2&3 and click here for the detailed manufacturing steps and addtional information about challenges).
The linear actuator PAM (click here to see manufacturing steps) works as the jellyfish muscle. Once filled with air it contracts and emulates the recovery stroke, when no air is applied it mimics the power stroke of the jellyfish.
The prototype shows a similarity to the movement of a jellyfish and it is waterproof as shown in the video on the right. Space for improvement exists, thus future work includes adding a cover layer similar to the bell shape of the jellyfish, automating the actuation system and amplifying the mechanism strokes.

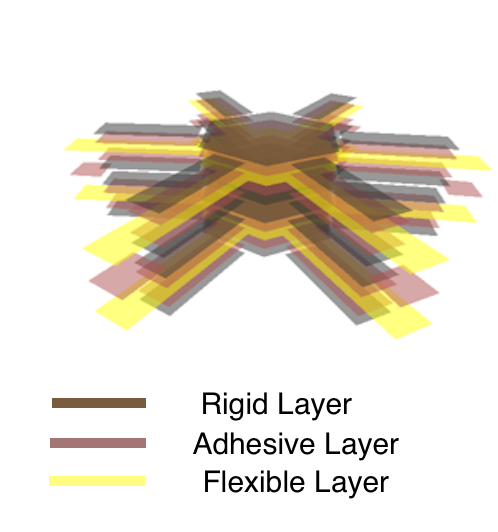


using Sarrus linkages


The orange filament seen in the picture is the PAM.
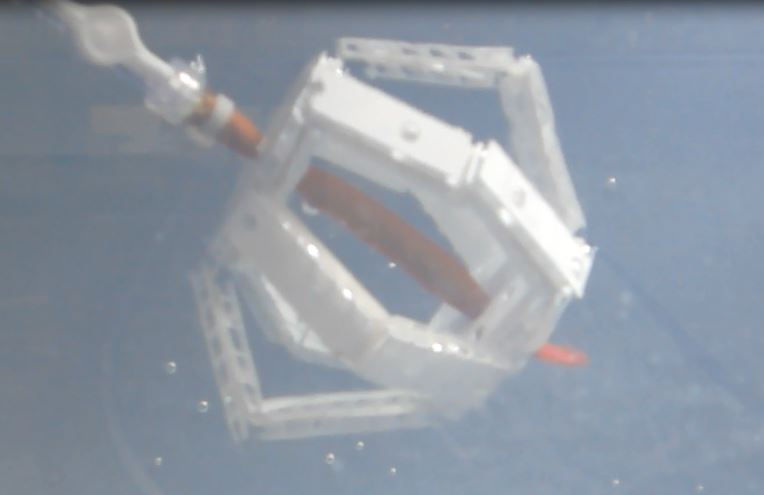